Introduction : Arrivée à Mananjary, après 26h de taxi brousse ! Durée « normale » du trajet 15h environ, mais avec un taxi peu puissant et une panne de 6h, le temps s’est vite allongé… mais voyons le bon côté des choses, j’ai pu contempler le paysage splendide sur la route, entre les vastes rizières des hauts plateaux et la forêt tropicale à l’Est du pays.
Je pose mes bagages à l’hôtel CHEZ YVONNAH où je vais séjourner pendant ma mission et prends mon déjeuner avec Dieudonné. Le cadre est agréable, un beau jardin fleuri, des bungalows originaux en bois et la cuisine est délicieuse.
Départ ensuite avec Dieudonné en direction de la ferme pour me familiariser avec le trajet que je vais emprunter dès le lendemain à vélo et ce, tous les jours ! Découverte du chantier : charpente arrivée sur site, les fondations, longrines et la couche inférieure du dallage réalisées. Nous avons également profité d’un dîner en regardant le beau coucher du soleil sur le canal du Pangalane.
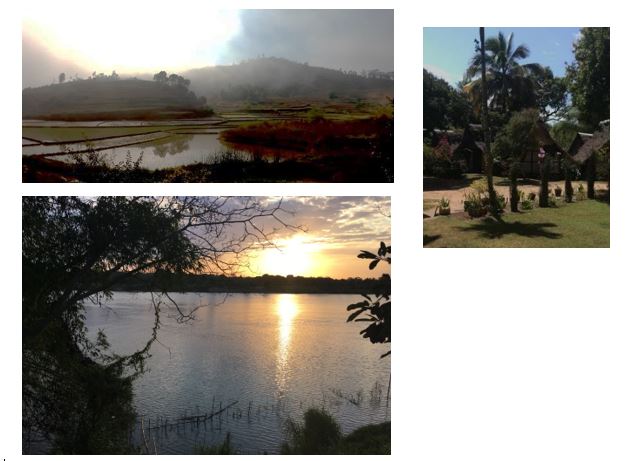
ACTIVITES REALISEES :
Nous avons consacré le premier jour à décharger le camion, vérifier l’implantation des fondations et de faire une réunion de chantier avec l’entrepreneur et Dieudonné, le représentant de PACHAMAMA. Sur chantier, il n’y a pas de machines à café, il y a mieux : la noix de coco !
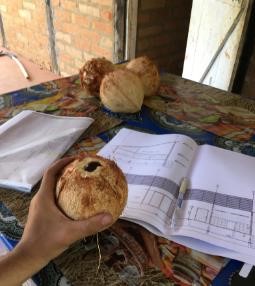
Déchargement du camion qui a livré les pièces de la charpente et de la couverture
Avant le déchargement, j’ai demandé au chef de chantier de dégager une aire de stockage proche du bâtiment afin d’optimiser les déplacements des pièces de charpente. Ensuite nous avons mis au sol des bastaings bois pour protéger les pièces métalliques et faciliter le levage.
Faute de machines de manutention, le camion est déchargé à la main, il est donc nécessaire d’optimiser les mouvements, pour cela j’ai demandé aux équipes de poser les pièces de la façon LIFO par rapport à l’ordre de pose que nous avons convenu initialement.
Vérification de l’implantation des réservations avant le début de la pose des poteaux
Avant de poser les poteaux, nous avons procédé à la vérification de l’implantation des réservations dans les fûts réalisés précédemment.
Nous avons mis en place des tendeurs au niveau des axes du bâtiment, faute de GPS et laser d’équerrage, nous les avons réglés afin d’obtenir les mesures exactes des côtes de chaque rectangle.
Nous avons constaté des écarts très minimes de l’ordre d’un centimètre, qui seront rattrapés par le jeu qui a été prévu dans les réservations. J’ai été surpris par le degré de précision atteint sans matériels moderne de mesure et d’implantation.
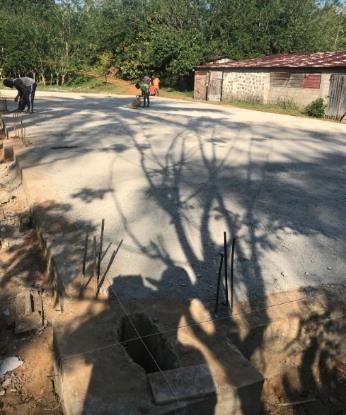
Levage et pose des poteaux
La charpente est constituée de 12 poteaux, 6 unités de 2m de hauteur, faciles à manipuler par 4 personnes. Les plus grands poteaux font 6m de hauteur (6 unités) font environ 500kg, la tâche s’annonce difficile sans utilisation de grues ou machines de levage, mais nous avons réalisé cela avec les moyens du bord : Cordes, bastaings bois et 32 personnes !
Afin de sécuriser le levage, nous avons décidé monter 4 groupes : le premier groupe soulève à la main la tête du poteau, puis positionne, bloque et stabilise le pied du poteau, en même temps les 3 autres groupes tirent les cordes sur 3 axes afin de stabiliser le levage. Ainsi, nous avons pu lever les 12 poteaux en une seule journée.
Nous avons ensuite procédé à la vérification des niveaux de platines et de la verticalité des poteaux avec le fil à plomb, le niveau est vérifié avec la technique du tube à eau, une découverte de ma part.
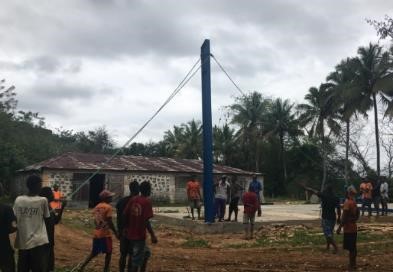
Nous avons ensuite procédé à la vérification des niveaux de platines et de la verticalité des poteaux avec le fil à plomb, le niveau est vérifié avec la technique du tube à eau, une découverte de ma part.
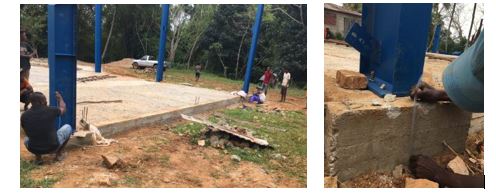
Fabrication des supports bois
En parallèle du levage des poteaux, une équipe de deux personnes monte les tréteaux et poteaux bois provisoires de support de levage de charpente. J’ai demandé de fabriquer des tréteaux de 3m de hauteur (1/2 hauteur maximale de la couverture) afin de pouvoir poser dessus les poutres lors du levage.
Une fois le premier tréteau monté, j’ai constaté qu’une seule croix a été mise dans la partie supérieure, je leur ai demandé de rajouter une autre croix inférieure afin de transmettre les efforts vers les pieds, rigidifiant ainsi l’élément. Ces pièces nous servirons également d’échafaudages pour la réalisation des murs en maçonnerie.
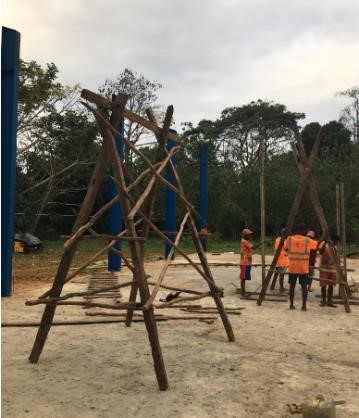
Levage et pose des poutres
Le mercredi nous avons commencé la tâche la plus difficile du chantier : lever les poutres (environ 500 kg chacune) à 6m de hauteur. La charpente est constituée de 6 poutres de 10,7m de longueur, composées de 2 pièces 4&6m.
Nous avons commencé par tester deux méthodes de levage des poutres :
La première consiste à monter et fixer séparément les deux pièces de la poutre sur les poteaux respectifs puis les assembler en hauteur, le but était d’alléger la charge de levage.
La deuxième poutre a été assemblée au sol, puis soulevée et fixée sur les poteaux.
Résultat : la deuxième méthode est retenue car beaucoup plus rapide et moins fatigante.
Nous levons les poutres avec la méthode suivante :
Levage de l’extrémité la plus haute (file B) par tirage par cordes coulissant dans des mousquetons (25KN) fixés en tête des poteaux en aidant avec un soulèvement à la main à hauteur d’homme puis blocage par poteaux bois et tréteaux provisoires au fur et à mesure du levage, l’extrémité basse (2m Ht) est levée à la main. Bien évidemment, les poutres sont toujours tenues en tête par des cordes afin de sécuriser au maximum le levage.
C’est ainsi que nous avons pu monter la charpente de 9 tonnes en 4 jours (y compris les pannes), un temps plutôt satisfaisant pour des travaux de telle taille et ce sans machines de manutention.
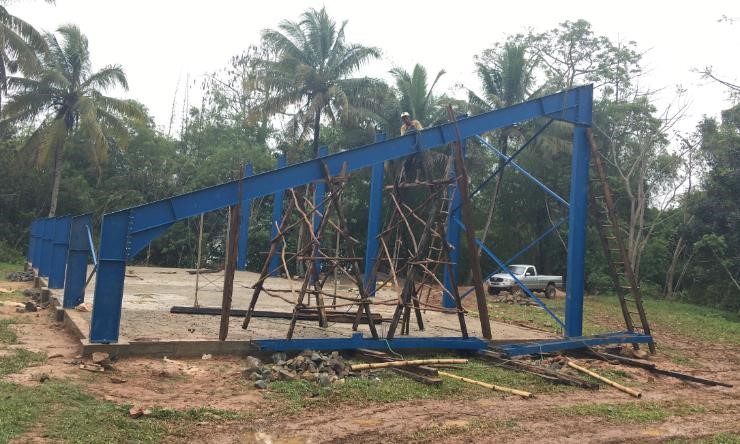
Nous avons consacré la deuxième semaine à la pose de la couverture, la fabrication des parpaings, et au montage des murs en maçonnerie.
Dès le début de la pose des tôles de couverture, j’ai remarqué que l’équipe disposait d’une simple visseuse, très insuffisant pour tenir la cadence souhaitée. J’ai donc demandé au chef de trouver une autre visseuse afin de pouvoir avancer plus vite ; une équipe qui monte les tôles et les fixes en quatre points, et un ouvrier suit avec la deuxième visseuse pour mettre en place le reste des vis de couture et fixations.
Pendant ce temps, quelques ouvriers fabriquent les parpaings, une équipe approvisionne le sable, le ciment par transport fluvial avec le bateau de l’entreprise et l’eau depuis le canal qui se trouve à côté du chantier, puis les repartissent sur les quatre ateliers de parpaings. Ces derniers sont constitués par deux ouvriers qui mélangent le sable, ciment et l’eau et fabriquent des parpaings à l’aide d’un moule métallique.
Les blocs de parpaings sont dosés à 300 kg/m3 en ciment, les sacs de ciment font 50 kg et 0,05 m3, et l’aide de bidons de 20L on dose le mélange.
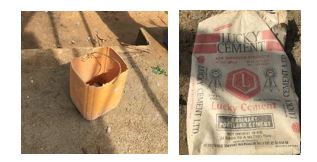
La réalisation de parpaings par des moules, le démoulage semble facile, cependant, cela nécessite un savoir-faire et technique qu’on apprend avec la pratique. Ci-dessous la photo de mon premier parpaing après 4 blocs ratés !!

En Conclusion…
Cette expérience a été très enrichissante. Du côté humain, j’ai apprécié la gentillesse et la bonne humeur des ouvriers sur chantier et des malgaches en général. Sur le plan professionnel, j’ai appris des vielles techniques que nous avons oublié en dépit des moyens technologiques actuels.
Les gens ont une vision de la vie différente des pays occidentaux. Malgré la difficulté des conditions de vie dans le pays, la gentillesse, l’entraide, le « no-stress », la musique et la danse sont toujours au rendez-vous ! j’ai été surpris de voir les ouvriers faire des blagues et rigoler même pendant les moments les plus difficiles du chantier comme pendant le levage des poutres avec les risques de l’opération. Et de les voir danser en groupe à la fin de la journée sur des chansons locales.
Au départ, vu la crise économique de la ville et le taux élevé du chômage, je pensais qu’il allait me falloir beaucoup d’efforts pour motiver les ouvriers qui sont rémunérés à la semaine, et qu’ils fassent « durer » le chantier, dans leur intérêt financier. Finalement, je suis fier des équipes, de la cadence et de la qualité des travaux réalisés pendant ces deux semaines sur le chantier dans lequel, j’étais à la fois encadrant et ouvrier. Mais l’exploit est grâce au dévouement des jeunes ouvriers et leur intérêt à apprendre de nouvelles techniques de construction.
Par ailleurs, l’éloignement de la ville de Mananjary et l’absence de chantiers de grande taille dans la région, ne permettent pas de se procurer facilement des engins de chantier telles que des grues et nacelles qu’il faudrait commander depuis la capitale, moyennant des frais de transports importants. J’ai également remarqué l’absence des autorités de contrôle de chantiers. En conséquence l’aspect sécurité sur les chantiers de la région reste à améliorer en termes d’engins de manutention et d’EPI. En effet, à mon arrivée, peu d’ouvriers portaient de gilets, mais j’ai réussi à les convaincre de l’importance des EPI et de convaincre le chef d’entreprise de leur en fournir. Ce dernier est parti à Tananarive pour acheter des gilets et gants puis les ramener une semaine après, et me promettant la fourniture de bottes et casque plus tard.
Enfin, c’était avec les larmes aux yeux que je quittais le chantier mon dernier jour, en passant le relais à Maud en lui souhaitant bon courage.